【図解】新たな設備保全「予知保全(予兆保全)」とは?メリット・デメリットを解説
- sakurai-column
- 3月28日
- 読了時間: 7分
更新日:4月21日

製造工場ではさまざまな設備が稼働しており、中には昼夜問わず稼働しているケースもあります。これらの設備を安定して稼働させるためには設備保全が欠かせません。
これまでは故障したら修理・交換を行う「事後保全」、決められた計画に沿って点検・メンテナンスし故障を未然に防ぐ「定期保全」が主流でした。
しかし、近年では人材不足や働き方改革による残業時間の制限、それに伴うAI活用・IoT化の浸透により、新たな保全方法が注目されています。それが「予知保全」です。
この記事では、「予知保全」の意味や、「事後保全」「定期保全」との違い、メリット・デメリットについて解説していきます。
1. 予知保全とは(PdM:Predictive Maintenance)
予知保全とは、設備の状態をIoTセンサーやAIで常時監視して故障やトラブルを予知し、最適なタイミングで点検やメンテナンスを行う保全手法です。
不具合の兆候を感知して保全するため、「予兆保全」とも言われています。
※IoT(Internet of Things)…対象の状態を電気信号に変換して、ネットワーク経由でデータを集める装置
2. 事後保全・定期保全との違い
設備保全は、大きく「事後保全」「定期保全」「予知保全」の3つに分類されます。
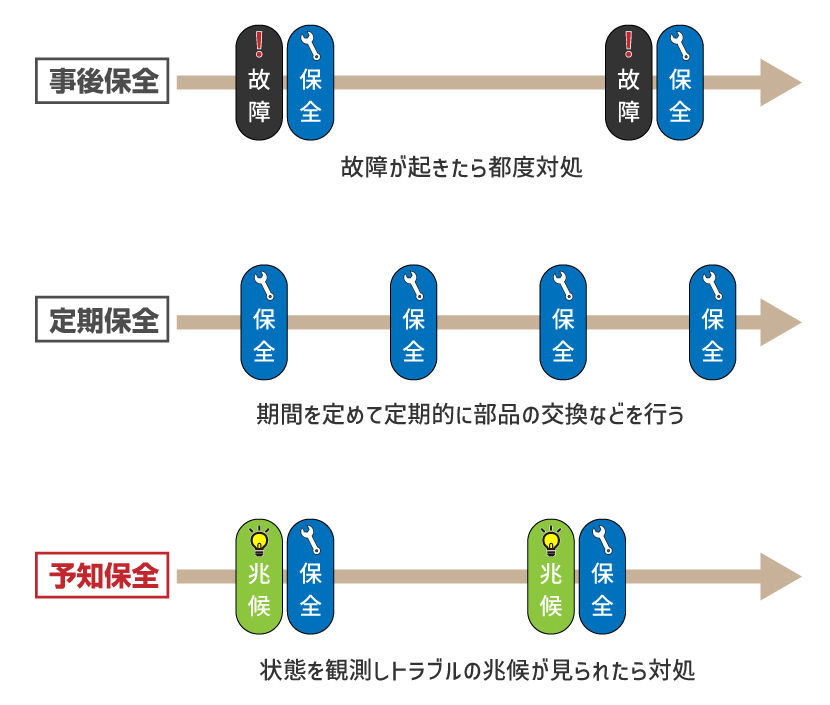
事後保全(BM:Breakdown Maintenance)
設備の故障や不具合が発生した後に修理や交換を行う手法です。
日々の保全作業が発生せず、機器や部品を寿命まで使い切ることができるため、使用できない時間があっても大きな損害がなく、すぐに交換できる設備(蛍光灯など)に適した保全方法です。
反対に短時間で修繕できないような故障に対しては、スムーズな対応ができず長時間のダウンタイム(稼働停止期間)が発生するため、設備の重要度に応じて選択する必要があります。
定期保全(TBM:Time-based Maintenance)
設備や機械が故障する前に、1か月、1年など決められた時間の間隔に沿って点検・メンテナンス・交換を行う保全手法です。
故障や不具合を未然に防ぐため、事後保全で起こりえる突発的な生産停止を回避することができます。
しかし、機器や部品の寿命に関係なく計画に沿ってメンテナンスを行うことで、まだ使用可能な部品を交換してしまう(オーバーメンテナンス)可能性があります。
また、事後保全に比べてメンテナンスの頻度が高いため、保全担当者の人件費や作業負担が増すデメリットもあります。
対して予知保全では、状態監視により“必要なときだけ”保全作業を実施できるため、保全担当者の作業負担や部品交換を減らすことができ、より高い生産稼働率の維持が可能となります。
3. 予知保全のメリット
■設備の部品交換を適切なタイミングで実施できる
定期保全では、メンテナンスの時点でまだ使用できる余地があっても決められた計画に沿って部品を交換することがあるため、部品代が余分に発生してしまいます。
一方、予知保全は設備を常に監視しているため、部品交換の適切なタイミングをシステムを通して確認することができ、部品代の削減が可能となります。
■ダウンタイムを短縮できる
定期保全でも故障による生産の停止を防ぐことができますが、部品の劣化だけが原因とは限りません。
設備が停止してから原因を究明し修繕を行っていると長時間のダウンタイムが発生してしまいます。
予知保全では、どの設備にどのような不具合が生じているのか具体的な情報を即座に把握できます。
そのため、原因究明に時間を取られることなく修繕作業に取り掛かることができ、ダウンタイムの短縮につながります。
■保全担当者の作業工数を最小限にできる
定期保全は設備の状態を問わず定期的に点検を行うため、生産規模が大きいほど保全担当者の人員を必要とし、また保全担当者の作業負担も大きくなります。
その点、予知保全であればシステムが設備不具合の有無を常時監視するため、最低限の人員で保全作業にあたることができます。
作業工数も大幅に減ることで保全業務が省力化でき、浮いた人件費を他に充てることが可能となります。
■保全担当者教育にかかるコストを削減できる
熟練の保全担当者であれば、長年の経験から不具合を見つけたり、故障前に対応したりすることが可能ですが、経験の浅い社員が同等の技術を習得するには多くの時間を要します。
予知保全システムによって自動で不具合を検知できるようになれば、入社したばかりの社員でも即戦力となり、熟練者の経験に依存しない仕組みづくりができます。
4. 予知保全のデメリット
■監視システムを導入するコストがかかる
予知保全の実施には、設備を監視するシステムを導入する必要があるため、初期費用がかかります。
しかし、メンテナンスコストや教育コストの削減など、予知保全を行うことで減らせるコストも多くあります。
システム導入によって必要になるコストと削減できるコストをしっかりと把握し、費用対効果を十分に検討することが大切です。
■十分な学習データを必要とする
AIや機械学習を活用した予知保全では、学習データの量が多いほど精度が高まります。
十分なデータが蓄積されていない初期段階では予測精度が不十分な場合があるため、はじめて予知保全システムを導入する際には、それらを念頭に置く必要があります。
必要なデータは設置する設備によって異なりますが、通常時・異常時それぞれの振動や温度、音、電圧などが挙げられます。
5. 簡単・安価にはじめる設備の「見える化」
予知保全システムの導入を検討する中で、「AIやIoTは難しそう」と感じる方も多いのではないでしょうか。
しかし、実際には、手軽かつ低コストで導入できるソリューションも多く存在します。
その一つが、センサーを設備に取り付けるだけでデータを自動で取得・送信し、異常の兆候をリアルタイムで把握するシステムです。
たとえば、弊社が提供する『e-無線巡回』は、温度と振動加速度の傾向監視に特化した設備監視システムです。
コンプレッサーやポンプ、モーターなど、回転機械の異常な振動や温度変化をセンサーが察知し、それらを送られてきたデータから遠隔で確認することができます。
親機・子機・ソフトがセットになっているため、パソコンとLANケーブルがあればすぐに現場監視を始められます。
現場に行かなくても設備状態が把握でき、点検業務の効率化やトラブル防止に役立ちます。

『e-無線巡回』は2017年の発売以来、導入実績300社以上を超え、多くの予知保全に貢献しております。
「まずは手軽に始めたい」「低価格で多数の機器を監視したい」といったニーズに応える、導入しやすいスタートツールです。
6. まとめ
製造現場は特に人材不足が深刻であり、限られた人員と時間の中で仕事を回さなければなりません。予知保全システムはそのような職場環境の改善を促し、生産稼働率の向上に役立ちます。
導入コストや導入手順、運用までに必要な期間は導入するシステムによって異なりますので、しっかりと情報収集・比較検討をしていくことが大切です。
弊社では、専任の製品担当者がヒアリングを行い、責任を持って対応させていただきます。予知保全に不安をお持ちの方や少しでもご興味を持っていただけた方は、ぜひお問い合わせフォームよりご相談ください。
「まずは製品について詳しい情報が見たい」というお客様は、下記よりe-無線巡回専用サイト、製品カタログをご覧ください。
執筆者紹介
下原 えみ(shimohara emi)
2024年桜井株式会社に入社。社員研修後にマーケティンググループへ配属。社会人生活もWEBマーケティングもまさにゼロからのスタートとなるが、どちらも両立するべく日々勉強に励んでいる。新入社員ならではの視点と丁寧な文章力を武器に”ためになる”コンテンツ記事作成を目指す。最近はドラマ相棒を見るのが至福の時間。
このコラムは、当社 営業推進企画部の出展商品担当者へのインタビューを基にWEB編集担当部門にて執筆・監修を行っております。